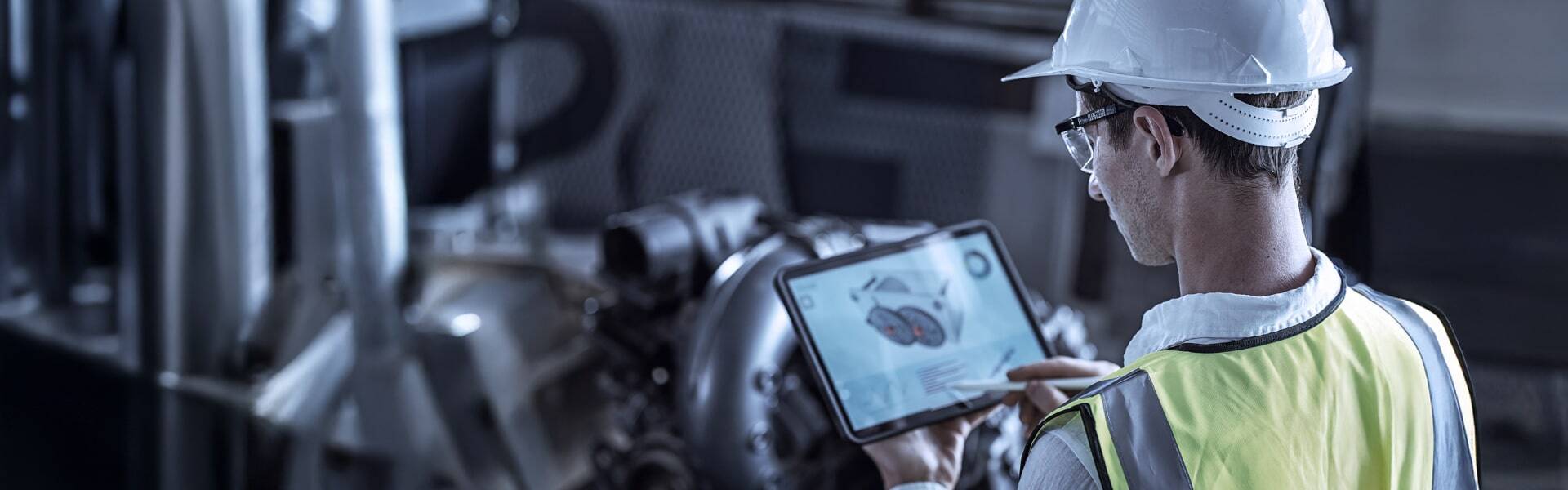
Efficient Software for Outgoing Goods Inspection
Reduced inspection and documentation costs, fewer customer complaints
Flawless Delivery Quality
Integrated certificate creation, inspection orders directly from the ERP system
With our outgoing goods inspection software, CASQ-it OGI, you can monitor the final quality before dispatch. Delivery certificates document flawless delivery quality. In the event of defects, the software automatically initiates corrective actions, triggers re-inspections and documents repair loops. Using dynamic inspection severity adjustments, you can reduce your inspection costs by concentrating inspections on areas with the highest risk of defects. Powerful analyses reveal improvement potential, helping you learn from defects.
CASQ-it OGI can operate as a standalone solution or seamlessly integrate with other CASQ-it modules — providing a tailored solution to meet your specific requirements.
Benefits of Our Outgoing Goods Inspection Software
How CASQ-it OGI supports you in ensuring quality in outgoing goods
Outgoing Goods Inspection in the Material Process
Delivery Preparation
The outgoing goods inspection software and your ERP system are tightly integrated for maximum efficiency: production and delivery orders from your ERP system automatically generate the corresponding inspection orders, triggering the final quality inspection.
Alternatively, you can create inspection orders directly in CASQ-it OGI. Inspectors then simply start the inspection order from the inspection order list and proceed with the outgoing goods inspection.
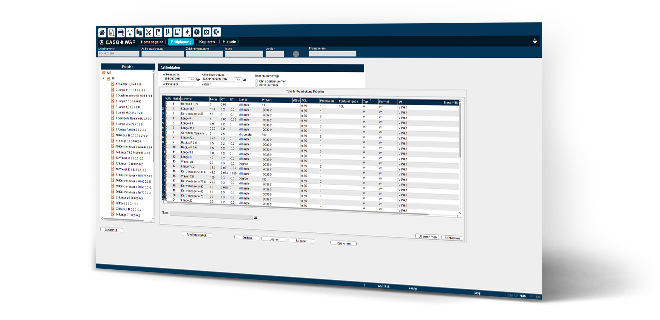

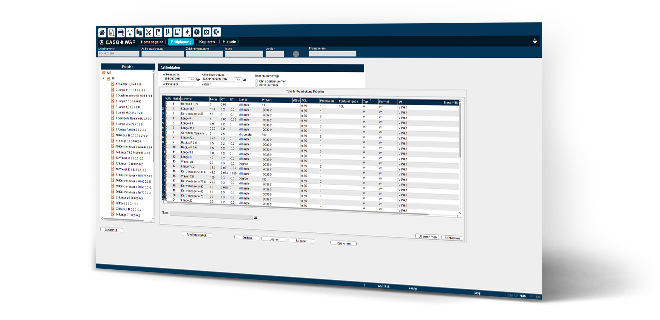
Outgoing goods inspection
Dynamic inspection severity adjustments help reduce inspection costs by ensuring that checks are performed only where defects are likely to occur. During inspections, employees are fully supported with specifications, drawings, supplementary images and documents.
In the event of a defect, error catalogs guide employees through the commenting process. The outgoing goods inspection software automatically initiates rework loops and monitors compliance with repeat inspection requirements.
Take Your Outgoing Goods Inspection to the Next Level
Delivery Certificates
CASQ-it OGI completes your shipping documentation: delivery certificates provide documented proof of defect-free delivery, listing all agreed-upon characteristics. Finished products are labeled with approval tags for easy identification.
Internal certificates, customizable lists, detailed analyses and the development of your quality metrics provide transparent insights into your delivery quality. Cost analyses offer a solid basis for evaluating production defects and rework efforts.
Analyses
Only identified defects can be prevented — that's why the integrated analytics tools in the outgoing goods inspection software provide insight into the quality history of your products.
With defect hotspot and root cause analyses, histograms, ppm and capability metrics, as well as customer-specific and independent analyses, you continuously uncover improvement opportunities.
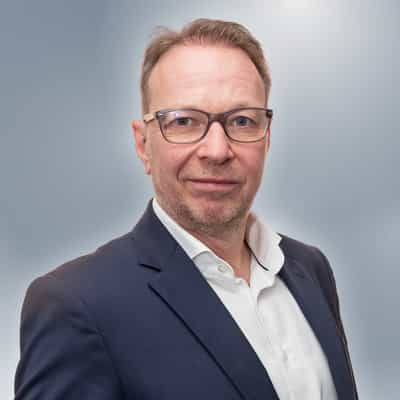
Your Point of Contact
Would you like to find out more about our digital solution for quality management?
With his many years of experience, Guido Goldammer is your ideal point of contact for all questions about this topic.
FAQ About Our Outgoing Goods Inspection Software
CASQ-it OGI reduces inspection efforts through dynamic inspection severity adjustments, focusing only on areas where defects are likely. The software also provides automated inspection orders generated from the ERP system and intuitive user guidance for faster processing.
The software generates delivery certificates to document flawless delivery quality and integrates them into shipping documents. Approval labels are used to mark inspected products, while customizable internal certificates and result lists offer additional flexibility.
CASQ-it OGI provides a wide range of analysis tools such as defect hotspot and root cause analyses, histograms, ppm values and capability indices. These tools help identify defect sources and continuously improve delivery quality.
The software streamlines processes through automatic quantity feedback and inspection orders, reduces documentation costs, and boosts efficiency with intuitive user guidance and integrated tools like drawings and defect catalogs.
Yes, CASQ-it OGI seamlessly integrates with ERP systems and CASQ-it modules such as Complaint Management and Gauge Management. This integration ensures smooth data flow and optimized process control in quality assurance.