WELP Gruppe
CAQ CONTROLS ARMORED VEHICLE ASSEMBLY PROCESS
For the WELP automotive group, production digitalization is not a buzzword from the Industry 4.0 dictionary, but rather a concrete step towards the future. At the Farmingtons Automotive site in Georgsmarienhütte, important stages in the assembly process are directly controlled by their quality management software. An intelligent torque wrench receives the target values directly from a test order. All the operator now has to do is to tighten up the screw whilst the wrench simultaneously measures the applied force and sends the result to a test log – thus combining the assembly process with the quality assurance process in one single process step.
The WELP Group is a full-service supplier for the automotive industry and is split into five companies: Farmingtons Automotive GmbH, IndiKar Individual Karosseriebau GmbH, pgam advanced technologies Ltd, Dressel + Höfner Automotive GmbH and S.C. Dressel + Höfner International S.R.L. – spread across six locations. Four of these sites are located in Germany, including the site of the Group’s origins, in Georgsmarienhütte. WELP currently employs a total of around 750 people. They offer their customers in the automotive sector numerous services, ranging from product development, to the manufacture of prototypes and tools and series production. In addition, they produce special vehicles for customization in the luxury segment, as well as vehicles designed to provide special protection, particularly armor-plated vehicles. Their customers include OEMs, such as Daimler, Audi, Porsche, and Bugatti.
CERTIFIED SPECIAL PROTECTION SOLUTIONS
At Farmingtons Automotive in Georgsmarienhütte, solutions are developed to provide special protection and safeguard passengers from bullets and explosive attacks. Their clients include police forces and UN organizations. The vehicles, mostly Toyota Land Cruisers, are elaborately retrofitted with armor plating, reinforced chassis, and other additional safety devices, such as fire extinguisher and run-flat tire systems.
When producing these armored solutions, a laser is used to precisely cut out the individual parts of the armor – which was specially developed by Farmingtons – from a steel plate. These individual parts are then welded together to form modules. Once an armored kit has been completed, it is then dipped into an immersion bath to coat it to protect the steel from corrosion prior to bolting the modules into the vehicle.
All of Farmingtons’ armored solutions are certified through official ballistics testing according to VPAM BRV2009, VPAM ERV2010 and STANAG 4569. The structural changes are hardly noticeable – neither inside nor out.
QUALITY MEANS SAFETY
In order to guarantee the safety of their passengers – even in extreme situations, the top priority at Farmingtons Automotive is to ensure high quality levels during the production process. Back in 2017, when WELP acquired the Dressel + Höfner GmbH & Co KG and Dressel + Höfner International SRL Medias (Romania) companies, both of these companies had already been using the CASQ-it CAQ solution provided by Böhme & Weihs Systemtechnik GmbH & Co KG for over 10 years. In 2018, the positive experience that had been gained in controlling the quality in the respective incoming goods sections, in recording deviations in the production process, in evaluating suppliers, in processing complaints and in administering inspection devices also convinced Farmingtons Automotive – who have been deploying CASQ-it ever since.
As part of the quality assurance process, Farmingtons checks its products for deviations at special measuring stations. However, previously, it was impossible to check the torque applied to screw joints. This meant that it was impossible to check whether the specified amount of torque had been applied to a screw joint using conventional techniques. Every time a torque wrench is used to carry out a check, this increases the total Nm value. In former times, the question of whether an operator had actually tightened a screw using the correct amount of torque depended solely on his skill and diligence. The quality manager had to simply trust the entries in the respective inspection logs. Even if the operators were well trained and worked conscientiously, an element of uncertainty remained, nonetheless – and this is something that any company would want to wipe out, particularly in highly sensitive areas, such as where parts of the chassis of an armored, off-road vehicle weighing several tons are bolted together. In June 2019, Farmingtons Automotive started work on digitalizing this area of production and enabling efficient torque verification during the assembly process – in collaboration with Böhme & Weihs.
Important assembly areas are controlled by the CAQ software using special test orders. Image: WELP Group
ASSEMBLY PROCESS CONTROLLED BY THE CAQ SYSTEM
What WELP required Böhme & Weihs to do was to be able to control assembly using intelligent torque wrenches via assembly/test orders. The plan was to transmit the assembly values for the screw joints directly from the test plan to the wrench via radio technology – and to have the wrench adjust itself accordingly. Once the torque wrench received the target value, it would be triggered and then automatically send the torque value measured back to the test log.
After having tested various digital torque wrenches from different manufacturers in the production environment, Stahlwille Eduard Wille GmbH & Co KG from Wuppertal was found to be a suitable tooling partner. The decisive factors were the compact design of the “Manoskop 766/20” torque wrench and its flexible open source software – making it possible to quickly integrate it into both the work processes of the operators and the CAQ system.
ALL SCREW JOINTS 100%-TESTED DURING THE ASSEMBLY PROCESS – WITH NO EXTRA EFFORT
Quality control is vital and unavoidable, but generally takes time. Anyone with experience in a production environment is aware of the fact that it is always more exciting to put something together than to have to check the work completed afterwards with a measuring device.
By intelligently combining an electronic torque wrench with CASQ-it, two separate work steps were reduced to just one. Whilst tightening the screws, the operator simultaneously carries out a quality check. And that is not all that happens: The test order also relieves the operator of the tedious task of having to set the torque wrench to the correct value for the next screw each time he has completed a step. This means that the operator always has a correctly adjusted tool to hand for every single work step. He can continue on through his working routine as usual and only needs to intervene if the software reports a deviation in the measured value.
Even if the specified value is only slightly exceeded, the operator will be prompted to undo the screw and to tighten it up again using the correct Nm value. Should the value be exceeded by too great an amount, the test station will prompt the operator to undo the screw and replace it with a new one.
All the measured values are entered into the test log, seamlessly documented and evaluated in real-time.
The operator can fully concentrate his work on the screw joints. The assembly process is automatically controlled and the measured values automatically recorded by the CAQ software. Image: WELP Group
SECOND TEST CRITERION RULES DEFECTS OUT
To rule out measurement errors, rotation angle measurements are also carried out in addition to the Nm measurements. Alongside the torque value, the tool also transmits the rotation angle over to the test station. This ensures that there is no premature triggering of the torque wrench before the screw has been correctly positioned.
You do not notice that this measurement is being taken in the background. The operator can concentrate fully on the torque and only receives feedback if the torque and angle do not match. In this case, the cause must be alleviated directly by the operator.
TRACKING ALL THE WORK PROCESSES – RIGHT FROM KICKING OFF THE PROJECT
Currently, the pilot project includes screw joints on the chassis and in the brake system. Depending on the vehicle model concerned, 70 to 85 features are currently being tested. To save the operator from having to complete all the screw joints in one work step, the respective test plans are divided into several test sequences. This allows the operator to interrupt his work in between individual work steps and to carry on working later on.
The number of features being tested is actually expected to increase manifold in the future due to plans to use intelligent torque wrenches for all the safety-relevant screw joints.
As the operators were directly involved in the implementation process right from the outset, there was already a high level of acceptance during the pilot phase. The real-time inspections have also considerably eased the burden on the employees as the test station now reliably guides them through the test procedure. Additionally, the operators are now developing a higher level of awareness both for their work processes and quality in general.
DESIGNED FOR GROWTH
The excellent cooperation with Böhme & Weihs in getting the test station up and running facilitated a smooth integration into WELP Group’s quality control system. Now, the scope of application for controlled assembly through test orders can be extended to other areas – and investments in additional equipment and respective test stations gradually increased. The Georgsmarienhütte site is currently expanding its production capacity by adding a new factory hall. This is expected to be completed around mid-2020. Even at this early stage, it is planned to install more torque measuring stations in this hall.
SUMMARY
In collaboration with Böhme & Weihs, the WELP Group has taken an important step towards optimizing their production processes: During the production of armored vehicles, the CAQ software now allows them to check everything 100% in areas which are particularly relevant to safety – with the actual assembly work for the operator now being considerably easier through the support provided by the CASQ-it software. The fact that immediate feedback is provided in the event of a deviation in the measured values has led to an increase in general quality awareness, whereby this method of working also eliminates numerous potential defects right from the word go.
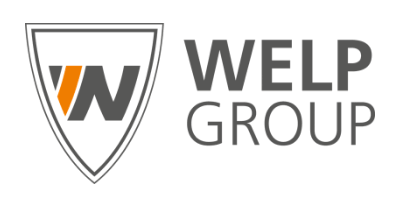
Industry: Automotive
Sites: Georgsmarienhütte, Germany
Producs: Product development service, prototype and tool construction through to series production and special vehicle construction, for individual special equipment in the luxury sector as well as special protection vehicle construction, in particular vehicle armouring.
Employees: Around 750 employees