Wilhelm Schumacher GmbH
STATISTISCHE PROZESSSTEUERUNG – KONSEQUENT BIS HIN ZUM MASCHINENSTOPP
Ob Erstteilprüfung, Letztteilprüfung oder laufende fertigungsbegleitende Prüfung: jede Prüfung ist unverzichtbare Grundlage, um die Fertigungsqualität zu überwachen und Prozessfehler zu vermeiden. Für eine zielgerichtete und zuverlässige Statistische Prozessregelung (SPC), gilt es, die vorgegebene Prüfsystematik unter allen Umständen einzuhalten. Um das zu gewährleisten, entschied sich ein Hersteller von Verbindungselementen für einen radikalen Lösungsweg: Nur wenn das CAQ-System bestätigt, dass alle geforderten Qualitätsprüfungen erfolgt sind, kann weiter produziert werden. Bleibt die Bestätigung durch das CAQ-System aus, erfolgt der sofortige Maschinen-Stopp.
Mit 34 Jahren gründete der Namensgeber Wilhelm Schumacher 1906 die Wilhelm Schumacher GmbH im nordrhein-westfälischen Hilchenbach. Zuerst mit Fokus auf Befestigungselemente wie Dübel, Haken und Ösen und später mit Kernkompetenz in der Herstellung von Verbindungselementen. Vom ersten Entwurf über die Werkzeugherstellung und Prototypenanfertigung bis hin zum Serienstart produzieren heute 180 Mitarbeiter bei der Wilhelm Schumacher GmbH sowohl Normteile und als auch individuelle Verbindungslösungen nach höchstem Qualitätsanspruch.
Tägliche Herausforderung: Die Verbindungselemente werden weltweit in Endprodukten verbaut, die schon alleine durch die Kategorisierung „Premium“ eine besondere Erwartungshaltung an die Qualität wecken. Kunden wie Miele und Liebherr in der Hausgeräteindustrie oder Daimler, BMW und Porsche in der Automobilindustrie legen die Messlatte hoch und kennen keine Kompromisse.
Genauso wenig wie die Wilhelm Schumacher GmbH selbst. Die Qualität der täglich rund 4,5 Millionen produzierten Schrauben, Kaltformteile und Stahl-Kunststoffverbundteile sichert das Unternehmen mit einem Qualitätsmanagementsystem, dessen Umfang und Wirksamkeit immer wieder selbstkritisch überprüft wird.
DURCHGÄNGIGES CAQ-KONZEPT IM GESAMTEN FERTIGUNGSPROZESS
So zeigte sich 2008, dass das Zusammenspiel aus ERP- und dem damaligen CAQ-System nicht mehr praktikabel war. Fehlende Funktionen, eingeschränkte Möglichkeiten zur Datenauswertung und der mangelnde Bezug zu den Anforderungen der Automobilindustrie, wie ISO/TS 16949 und zusätzlichen Kundenforderungen, versperrten dem Unternehmen einen ganzheitlichen Blick auf die eigene Qualitätslage. Eine Weiterentwicklung im Sinne des kontinuierlichen Verbesserungsprozesses war kaum noch effizient umzusetzen.
Die Geschäftsführung entschied: Anschaffung eines komplett neuen CAQ-Systems. Der passende Partner zeigte sich schnell in der Böhme & Weihs Systemtechnik und ihrem CAQ-System CASQ-it. Die untereinander kommunizierenden Module lenken und überwachen heute alle Qualitätssicherungsmaßnahmen von der Erstbemusterung über die Wareneingangs- bis hin zu den Fertigungsprüfungen, zentral koordiniert im Control Plan. Kommt es zu einer Abweichung, steuert das Reklamationsmanagement die konsequente Ursachenforschung bis zur Fehlerabstellung nach dem 8D-Verfahren. Das CAQ-System ist heute durch seinen prozessorientierten Aufbau derart in die Unternehmensabläufe integriert, dass es nicht mehr wegzudenken ist. Eine Tatsache, die auch immer wieder in Kundenaudits überzeugt – doch damit für die Wilhelm Schumacher GmbH nicht genug.
WERKERSELBSTPRÜFUNG: 900 STICHPROBEN PRO TAG
Im Zuge der selbstkritischen Überprüfung aller Qualitätssicherungsmaßnahmen entdeckten die Schraubenspezialisten 2014 weiteres Verbesserungspotenzial und zwar in der Fertigung: In den Produktionshallen stehen aktuell 75 Produktionsmaschinen, von denen jeder Werker zwischen 2 und 5 Maschinen betreut. Er ist für Betrieb, Rüstung, Erst-/Letztteilprüfungen sowie die fertigungsbegleitenden Prüfungen zuständig. Dies geschieht zu 100% in Werkerselbstprüfung. Ein umfangreiches und verantwortungsvolles Aufgabengebiet, bei dem die Mitarbeiter Gefahr liefen, den Überblick zu verlieren, ob und wann eine Qualitätsprüfung fällig ist. Nicht verwunderlich, denn pro Schicht finden 300 Stichproben statt – und das an mind. 5 Tagen die Woche im 3-Schicht-Betrieb.
Die Überwachung der Prüffrequenz erfolgt durch die CASQ-it Prüfstation, die mit farblich markierten Balken die Fälligkeit einer Prüfung anzeigt. Für den Werker eine absolut übersichtliche Lösung, die ihn zuverlässig zur seinen Qualitätsprüfungen auffordert – mit nur einem Problem: Die Qualitätsprüfungen finden zwar an speziell eingerichteten Messplätzen/ -räumen zentral der Fertigungsbereiche Kaltumformung, Walzen, Pressen, spanabhebende Nachbearbeitung und Wärmebehandlung statt, jedoch befindet sich die Fälligkeitsanzeige für die Prüfaufträge dadurch außerhalb des Blickfelds der Maschinenbediener. Selbst wenn jeder Mitarbeiter die anstehenden Prüfungen im Kopf hatte, führten Ereignisse wie Schichtwechsel, Werkzeugbruch oder Umrüsten dazu, dass sich die Prüfungen verzögerten und die Prozessqualität nicht mehr so engmaschig überwacht wurde, wie das Unternehmen es für sich forderte.
FEHLENDE QUALITÄTSPRÜFUNG STOPPT DIE MASCHINE
Das Qualitätsmanagement erkannte hier gleich Potenzial in zweierlei Hinsicht: Entlastung der Werker bei gleichzeitig steigender Prozesssicherheit. Gemeinsam mit dem langjährigen Partner Böhme & Weihs erarbeitete man eine Lösung, die in Audits bereits als einzigartig bewertet wurde. Möglich wurde das durch den hohen Funktionsstandard der CAQ-Lösung, die sich zudem auch noch flexibel einer völlig neuen Idee zur Qualitätsüberwachung öffnete:
Die Aufforderung zur Qualitätsprüfung verlagert sich von der zentralen CASQ-it Prüfstation direkt an die jeweiligen Maschinenterminals. Auf dem Terminal wird die Soll- und Ist-Zeit, einschl. der verbleibenden Restzeit des Prüfintervalls angezeigt, die mit der Maschinenechtlaufzeit gekoppelt ist. So weiß der Werker, wann die nächste Prüfung fällig ist und kann sich entsprechend darauf einstellen. Nach Ablauf des Prüfintervalls erscheint die Meldung „SPC-Prüfung erforderlich!“, ähnlich eines Pop-ups. Für den Mitarbeiter beginnt nun eine genau festgelegte Pufferzeit, die sogenannte Karenzzeit, innerhalb der er die Prüfung durchführen muss. Ist die Karenzzeit jedoch verstrichen und er hat die Qualitätsprüfung nicht durchgeführt, wird die Maschine automatisch gestoppt. Die Fertigung an dieser Maschine kommt dann vollständig zum Erliegen!
Das, was im ersten Moment übertrieben streng oder unwirtschaftlich erscheinen mag, ist für die Wilhelm Schumacher GmbH lediglich die logische Konsequenz aus dem eigenen hohen Anspruch: Ausschließlich qualitativ einwandfrei Teile zu liefern und alle dafür definierten Maßnahmen einzuhalten.
INTELLIGENTES ZUSAMMENSPIEL ZWISCHEN CAQ- UND BDE-SYSTEM
Überwacht wird das durch ein einzigartiges Zusammenspiel zwischen CAQ- und BDE-System. Über eine Schnittstelle tauschen sich die Systeme permanent aus und verfolgen so stringent die Einhaltung von Prüfumfang und Prüffrequenz:
Erstteilprüfung:
Zum Auftragsstart erhält CASQ-it durch das BDE-System die Auftragsdetails. Anhand der Teile- und Maschinennummer erzeugt das CAQ-System selbstständig den zugehörigen Prüfauftrag. Schritt für Schritt führt CASQ-it den Werker dann durch die Erstteilprüfung und unterstützt seine Arbeit mit Prüfanweisungen und hinterlegten Bildern. Ist die Prüfung erfolgreich abgeschlossen, gibt CASQ-it die Freigabe an das BDE-System. Erfolgt diese Freigabe durch das CAQ-System nicht rechtzeitig, das heißt nach Ablauf der Karenzzeit, stoppt die Maschine. Das gleiche Vorgehen gilt auch nach einem Werkzeugbruch, um auch in diesem Fall sicherzustellen, dass der Prozess vollständig überwacht wird.
Fertigungsprüfung:
Während der Fertigung erfolgt grundsätzlich nach 120 Minuten Maschinenlaufzeit eine Qualitätsprüfung. Führt der Werker die Prüfung nicht durch, stoppt die Maschine. Sie kann erst wieder in Betrieb genommen werden, wenn die Qualitätsprüfung durchgeführt wurde und CASQ-it die Freigabe an das BDE-System gibt.
Letztteilprüfung:
Wenn der Werker am Maschinenterminal „Auftrag beenden/unterbrechen“ wählt, wird automatisch eine Letztteilprüfung gefordert. Umgehend steht der entsprechende Prüfauftrag mit dem passenden Prüfplan am CAQ-Arbeitsplatz bereit. Erst nach der durchgeführten Letztteilprüfung im CAQ-System, kann der Fertigungsauftrag am Terminal abgemeldet werden.
WACHSENDE PROZESSVERANTWORTUNG FÜR DEN WERKER
Wirkt das Vorgehen im ersten Moment wie Kontrolle und Zwang, hat es sich für die Mitarbeiter bereits nach kurzer Zeit bewährt. Sie können sich vollständig auf die Maschinen in ihrem Verantwortungsbereich konzentrieren, da sie jetzt alle Prüfzeitintervalle direkt vor Ort im Blick haben. Die eingebaute Karenzzeit gibt ihnen ausreichend Flexibilität, um auf aktuelle Fertigungsereignisse zu reagieren.
Zudem reagiert CASQ-it durch die Verbindung zum BDE-System flexibel auf Fertigungsereignisse und passt die Prüffälligkeit entsprechend an. So verschiebt beispielsweise ein Maschinenstillstand die Aufforderung zur Prüfung nach hinten. Eine erhebliche Zeit- und Kostenersparnis, denn so prüfen die Werker nur, wenn in dem für die Prüffrequenz definierten Zeitraum auch tatsächlich produziert wurde.
Und die genaue Einhaltung der Prüffrequenz zeigt einen weiteren Vorteil: Jeder Werker ist für das Nachjustieren seiner Maschinen qualifiziert und bekommt seitens des Unternehmens auch das Vertrauen zugestanden, dies selbstständig durchzuführen – auf Basis der SPC-Prüfungen in CASQ-it. Die konsequente Einhaltung der Prüfintervalle zeigt dem Werker jetzt bereits in einem sehr frühen Stadium Prozessveränderung auf und zwar unmittelbar nach jeder Qualitätsprüfung über die Regelkarte. Hier sind Verletzungen von Eingriffsgrenzen natürlich ganz offensichtlich. Jeder Werker ist in der Lage, kleinste Prozessveränderungen in der Regelkarte zu erkennen und eine Verschiebung der Werte zu deuten. Mit dieser Informationsgrundlage und seiner Erfahrung als Maschinenbediener kann er die Maschine nachjustieren, um Toleranzverletzungen und somit Ausschuss und Fehlerfolgekosten zu verhindern. Für die Wilhelm Schumacher GmbH ein weiterer Schritt zur nachhaltigen Steigerung von Prozessqualität und Effizienz in der Fertigung.
ZENTRALE PROZESSINFORMATIONEN FÜR DEN FERTIGUNGSMEISTER
Die lebende SPC-Regelkarte ist jedoch nicht nur ein Werkzeug für die Werker, sondern auch für die Fertigungsmeister der einzelnen Produktionsbereiche. Im Zusammenspiel mit dem CASQ-it Schichtprotokoll haben sie einen Online-Rundum-Blick in die Fertigung. Denn das Schichtprotokoll verdichtet alle Qualitätsprüfungen in einer grafischen Gesamtübersicht: Jede Stichprobe wird mit einem Punkt dargestellt. Prüfereignisse, wie kommentierte Prüfung, attributive Fehler, Toleranz- oder Eingriffsgrenzenverletzungen und geskippte Merkmale sind deutlich markiert. Das Schichtprotokoll lässt sich individuell, beispielsweise nach Artikel, Merkmal, Maschine oder Prüfer filtern und der Auswertezeitraum entsprechend flexibel anpassen. Ein heute unverzichtbares Werkzeug für den Meister, der sich so zum Beispiel nach der vorangegangenen Nachtschicht innerhalb weniger Augenblicke einen umfassenden Blick zur Qualitätslage verschafft.
Ein Klick auf eine Prüfung im Schichtprotokoll öffnet alle Prüfdetails, die dazugehörige Regelkarte und Fehlersammelkarte. Durch diese besondere Übersichtlichkeit der Prüf- und Prozessinformationen kann der Meister heute auf einen Blick die relevanten Prüfereignisse erkennen und bewerten, sie eigenverantwortlich verfolgen und Probleme gemeinsam mit seinen Mitarbeitern direkt abstellen. Dieses Vorgehen hat sich bewährt, so dass der tägliche Blick in das Schichtprotokoll fester Bestandteil einer Arbeitsanweisung für alle Meister geworden ist.
PRÜFFREQUENZÜBERWACHUNG ÜBERZEUGT IM AUDIT
Die neue Lösung zur konsequenten Prüfintervallüberwachung mit Maschinenabschaltung überzeugt nicht nur die Wilhelm Schumacher GmbH sondern beeindruckte bereits auch schon einen Tier1-Kunden der Automobilindustrie im Rahmen eines Lieferantenaudits. Für den Auditor ein bisher beispielloser Beweis der Qualitätsanstrengungen auf dem Weg zum Null-Fehler-Ziel.
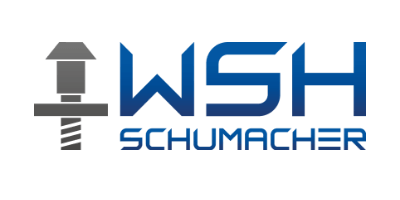
Branche: Automotive
Standorte: Hilchenbach, Nordrhein-Westfalen
Produkte: Normteile sowie individuelle Verbindungslösungen
Mitarbeiter: 180 Mitarbeiter