With the publication of the 1st edition of the FMEA Manual at the beginning of June 2019, an extraordinarily long coordination process, with numerous discussions, will draw to a close.
This means that, with immediate effect, the same FMEA specifications will apply to system developers, resp. original equipment manufacturers, serving the automotive industry and its suppliers in both Germany and North America. There have long been calls for harmonization – but will it now actually provide the simplification hoped for? What effects will the changes have on the daily work of the FMEA moderators? And which problems will remain? Winfried K. Dietz, General Manager of Dietz Consultants , takes a look at the development of the new FMEA Manual and evaluates the practicality of the 7 steps.
TAKING A LOOK AT THE HISTORICAL BACKGROUND
The background of the method description is extensive and straight to the point. Right at the very beginning, the idea was to coordinate harmonized FMEA evaluation catalogs between the AIAG and the German VDA (Association of the Automotive Industry). However, this quickly grew into something bigger, i.e. the concept of a common method description.
The path was long and arduous. I would just like to remind you here of the many times the publication was postponed and of the thousands of comments and “objections” to the draft (yellow print). This is a wonderful way of demonstrating the importance and, ultimately, the energies involved in FMEA. Having said that, the demands of FMEA are also huge: Identifying, evaluating and minimizing the risks during development. Looking into the future has always been a risky game.
Then, in June 2019, it had finally been achieved. For the first time, the AIAG and VDA committees released a joint FMEA method description for publication. It is certainly no exaggeration to quote this Manual as now being the global FMEA standard within the automotive environment.
BRIEF OVERVIEW OF THE 7-STEP CYCLE
The seven steps offer a complete and successful solution: They enable the entire risk analysis cycle to be covered in three categories.
- System analysis
- Failure analysis
- Risk communication
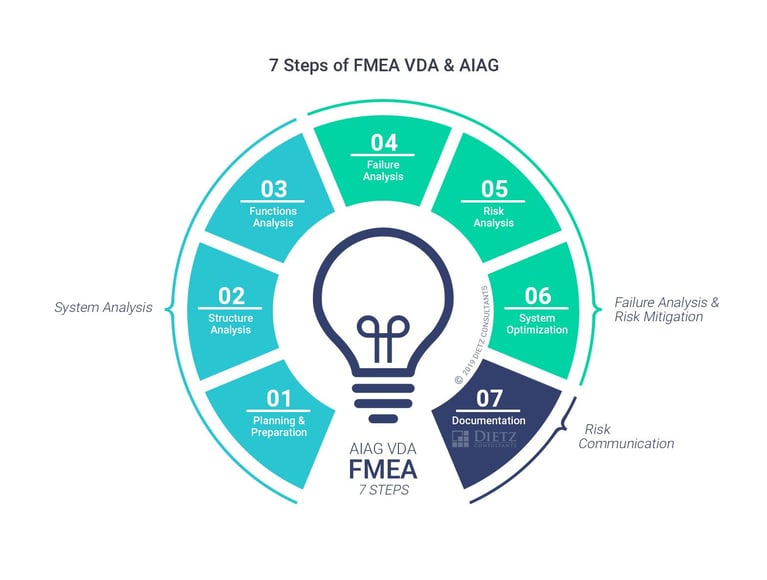
The 7 steps of FMEA (Source: Dietz Consultants)
These allow FMEA to be planned and realized in a chronological and logical manner. The 7-step approach will seem familiar to the “old users” of the 5 steps according to VDA. The core of the analysis still consists of the familiar 5 steps used in the previous VDA approach (from structural analysis to optimization). Step 1 “Planning and preparation” and the last step “Result documentation” have now been added. However, for previous AIAG users of FMEA, there have been a lot of changes. The focus has shifted away from forms to working in structures and linking up functions and malfunctions.
Also important is the fact that the Manual presents FMEA for 3 separate applications – each based on the 7 steps:
2. Process FMEA
3. Monitoring and System Response – MSR (presented as a supplement to the Manual)
The MSR supplement, in particular, is helpful, since the frequently discussed (and widely used) diagnoses and their integrated system responses are the subject of numerous discussions on how these should be treated in FMEA.
TASK PRIORITY INSTEAD OF RISK PRIORITY NUMBER
And last but not least, the Risk Priority Number (RPN) has been dropped – which was well overdue. On the one hand, this led to determining and attempting to adhere to “threshold values” – contrary to the specifications. On the other hand, risk assessments that were simply incorrect were also being produced because although the different combinatorics of the probability of occurrence and probability of detection, as well as the significance of the effects of the failure, may result in the same RPN, these apparently identical risk situations are actually far from being identical.
The solution is simple and straightforward: Task priorities (TP). These result from the combinatorics of the factors mentioned above, whereby the risk assessments boil down to three categories
- High
- Medium
- Low
A lot of work and effort went into the development of the TP logic. The idea is great, i.e. to prioritize the resources needed for the risk management process. As we all know, a Euro can only be spent once. At the end of the day, this also applies to risk management. The TP system will really face the test of time over the next few years when it is broadly applied on a global basis. Right now, things are looking “positive”. Ultimately, everyone is hoping that a successful approach has been introduced.
APPLICATION EXAMPLE
(Source: AIAG & VDA FMEA Manual, 1st edition 2019)
HELP WITH WORKING ON THE FINE DETAILS
The FMEA Manual contains numerous helpful details. Let me give you a few examples:
- The clarification of functions and requirements
- The clarification and description of roles
- The management’s obligation to provide information on the remaining risks
- The interaction of DFMEA and PFMEA
- The application of the two block diagrams (P and Boundary) within the context of FMEA
SUCCESS FACTORS OUTSIDE THE 7 STEPS
The success factors for efficient FMEA, however, are to be found beyond the 7 steps. These will continue to occupy us a great deal in the years to come. Let me give you some examples:
- The integration of FMEA into the data flow of tools flanking the product development process
- The analysis of complicated systems
- The analysis of software scopes
- Closed-loop approaches within the “big data” context – i.e. the backflow of sensor data from the field and manufacturing processes into the “lessons learned” processes
- A selective FMEA which operates at the right “altitude”
- The development of FMEA data models (from catalogs to “building block concepts”)
The above list is by no means complete. There is, therefore, still plenty to be done in the next few years before finally achieving a situation that will lead to development results which are both safe and sound and to series production start-ups that run smoothly.
WORK MANUAL FOR YOUR DESIGN AND PROCESS FMEA
Dietz Consultants provide Design and Process FMEA notebooks to support the work of FMEA moderators. In these, the 7 steps of FMEA according to VDA and AIAG and their associated tasks are described in a clearly structured manner. For each step, application examples provide you with helpful guidance for the practical implementation of your own risk management system.
Winfried K. Dietz
Winfried Dietz did a degree in Mechanical Engineering with a focus on Thermodynamics. In the following years, he continued to develop his knowledge of quality management, standard and industry requirements, processes and risk management. In 1990, he concentrated all his experience from a whole range of positions, including spells in the product development and quality management divisions at BASF AG, in “Dietz Consultants” – as founder and shareholder. Since then, he and his globally operating team have been supporting companies as consultants, moderators and trainers, helping these companies to further develop their quality and risk management activities.